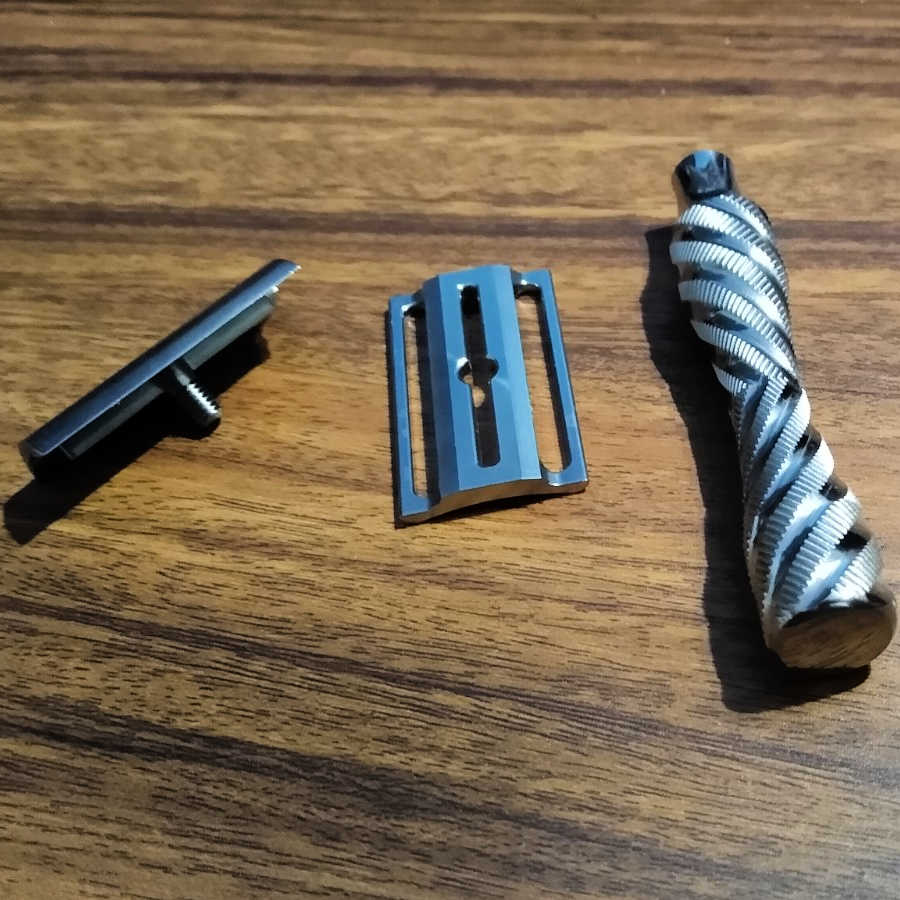
For many wet shavers, the quest for a perfect shave is marred by the annoyance of their safety razor succumbing to corrosion. It’s a surprising hiccup given that we often associate “stainless steel” with being impervious to such wear.
This article will dive into how different finishes affect the longevity and resilience of your trusted tool against corrosion. That sleek razor deserves more than just admiring glances; it may demand a strategy for enduring excellence.
Key Takeaways
- Different finishes on safety razors, like polished, matte, or coated, have unique effects on the razor’s resistance to corrosion and overall durability. Polished finishes reflect a sleek look and are less prone to corrosion but may show scratches easily. Matte surfaces hide wear but might need more frequent cleaning. Coated finishes provide extra protection against elements causing rust.
- The material of the safety razor impacts its longevity too, with stainless steel being a strong choice for resisting corrosion. However, other materials like brass and copper also offer benefits such as antibacterial properties despite their increased vulnerability to damage.
- Regular cleaning and proper maintenance are crucial in keeping your safety razor or straight razor in prime condition. Drying after use, storing it away from moisture, replacing worn parts promptly, and occasionally applying oil can extend the life of any finish on a safety razor significantly.
- Higher grades of stainless steel used in razors resist corrosion better than lower-quality options. For instance, grade 316L is more suitable for wet environments than grade 303 due to its superior corrosion-resistant properties.
- Being informed about how various factors affect durability will help you choose wisely between different safety razor finishes so that it fits both your aesthetic preference and practical needs for long-lasting shaving equipment.
The Importance of a Durable and Corrosion-Resistant Finish for Safety Razors
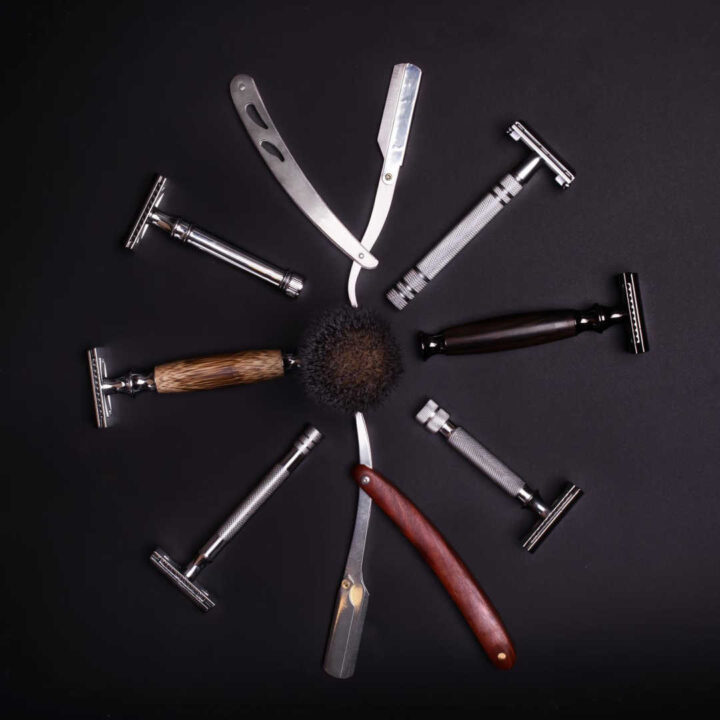
The finish of a safety razor can noticeably impact its durability and resistance to corrosion, affecting the lifespan and performance of the razor. Different types of finishes can influence how well the razor withstands exposure to water and other elements that could cause corrosion or other types of deterioration.
It’s important for wet shaving enthusiasts to understand how the finish of their safety razors can impact their overall shaving experience.
Types Of Finishes
Safety razors come in a variety of finishes, each offering a unique look and level of protection against wear. These finishes not only contribute to the aesthetic appeal but also affect how well the razor stands up to corrosion and daily use.
- Polished Finish: This glossy finish gives safety razors a mirror-like shine that’s visually striking. The smooth surface minimizes places where moisture can collect, lowering the risk of corrosion. However, polished surfaces can show scratches more easily and may require extra care to maintain their shine.
- Matte Finish: For those who prefer a less reflective look, matte-finished safety razors are ideal. This type of finish hides small scratches better than polished ones and often has a modern appeal. While it doesn’t hold fingerprints, it might not be as slick as polished finishes when gliding over wet skin during shaves.
- Coated Finish: Some safety razors feature protective coatings such as chrome plating or PVD (Physical Vapor Deposition) coatings. These layers enhance resistance to corrosion from water and shaving products. They can provide various colors, from classic silver to bold black or even blues and greens.
- Brushed Metal: Similar to matte finishes, brushed metal offers texture that masks wear while providing an industrial look. It does an excellent job resisting fingerprints and provides traction for wet hands.
- Bead-Blasted: A bead-blasted finish is achieved by propelling fine glass beads at the metal surface under high pressure, creating an even, non-glossy texture. This appearance catches fewer reflections but may require more frequent cleaning to keep its textured grooves free from soap accumulation.
Materials Used In Safety Razors
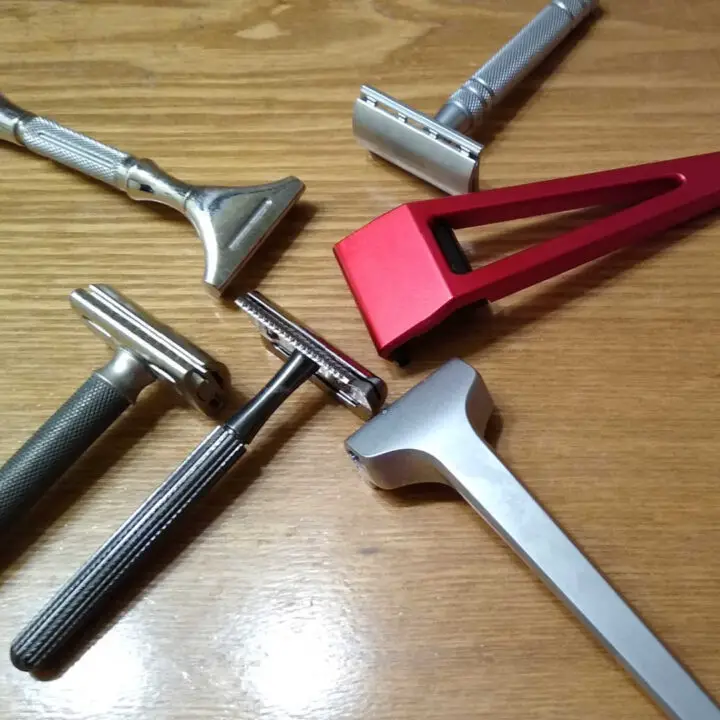
Choosing the right material for your safety razor can be a significant factor to both shaving performance and longevity. The metal must withstand frequent contact with water and resist corrosion over time.
- Stainless Steel: Among metals, stainless steel stands out for its strength and resistance to rust. Grade 303 might be more commonly used due to its machinability, but it’s less resistant to corrosion than grade 304. Conversely, “marine grade” stainless steel, such as grade 316L, tops the charts for corrosion resistance, making it a popular choice for high-quality double edge razors.
- Brass: This alloy isn’t just about looks; brass safety razors offer reliable corrosion resistance. However, brass is softer compared to tougher materials like stainless steel, which means they might not endure drops or rough handling quite as well.
- Copper: Safety razors made from copper boast impressive heat displacement and antibacterial properties. They’re eye-catching too but are generally softer than brass and could bend if accidentally dropped.
- Chrome Plated: A shiny chrome finish on a double edge razor (often over brass or copper) looks sharp, but there’s a downside to consider. The process of chrome plating can be harmful to both the environment and the workers involved in manufacturing these pieces.
- Damascus Steel: Known for its distinctive patterns similar to Wootz swords from ancient times, Genuine Damascus steel isn’t just about aesthetics—it’s tough with good wear resistance. Bladesmiths value this type of metal for knives and straight-edge razors due to its unique blend of durability and style.
- Titanium Alloy: For those who seek ultralight options without sacrificing durability, titanium alloy safety razors are an excellent choice. They combine strength with exceptional corrosion-resistant properties, perfect for anyone looking for a premium shaving experience.
The Problem With Rust (And Other Types Of Corrosion)
Corrosion can spell trouble for the longevity of your safety razor. Stainless steel, known for its durability, isn’t completely immune; it can succumb to surface rust. This happens when your trusty razor routinely battles water and dissolved salts, triggering a pesky chemical reaction (often called a “tea stain”) that leads to corrosion over time.
Some manufacturers might opt for lower-cost 303 steel to cut corners on expenses, but this move backfires as this type of steel is even more vulnerable to rust.
Regular shavers know the frustration: a once sleek razor blade tarnished by reddish-brown spots or pitting corrosion. These imperfections aren’t just about looks—they can lead to skin irritation or infections if not addressed promptly.
Shaving comfort requires smooth blades and clean edges free from corrosive damage. A corroded safety razor no longer cuts it—literally—in providing a close shave without risk of razor burn or ingrown hairs.
Frequency Of Use And Maintenance
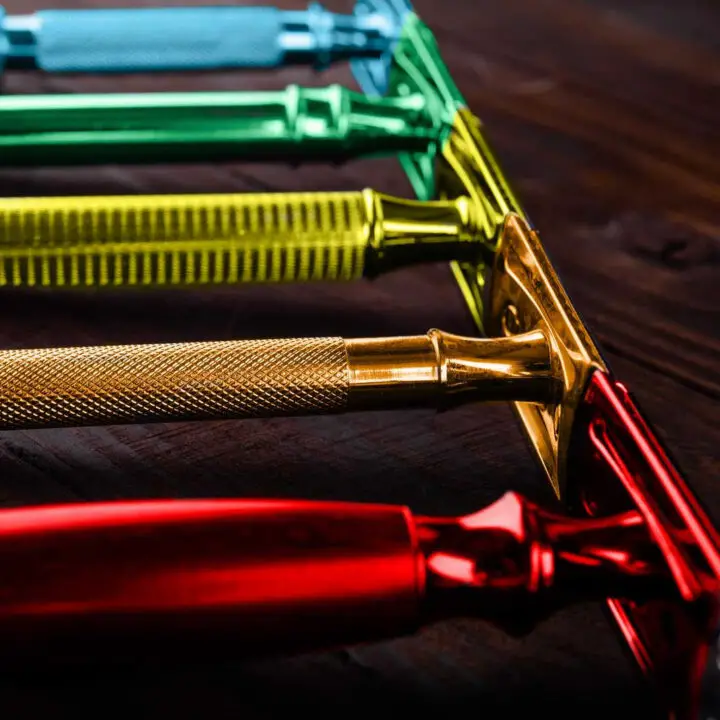
Consistent cleaning and maintenance play an important role in preserving the durability and resistance to corrosion of your safety razor. Cleaning after each use prevents the buildup of soap scum, skin oils, and hair residue, which can contribute to corrosion over time.
Proper storage also ensures your razor is thoroughly dried by storing it in a well-ventilated area away from moisture.
The frequency of use impacts not only the need for regular maintenance but also affects the potential wear and tear on the finish of your safety razor. As part of your routine, consider inspecting your razor for any signs of deterioration or damage that may require re-coating or re-polishing to maintain its longevity and resistance to corrosion.
Choosing The Right Finish For Your Safety Razor
Selecting the ideal finish for your safety razor is more than a matter of aesthetic preference; it can impact both the durability and resistance to corrosion. Here’s a breakdown of how different finishes hold up:
Finish Type | Pros | Cons |
Polished (Stainless Steel) | Modern, sleek look that’s visually appealing. Low maintenance requirements. High resistance to corrosion | Can show fingerprints and smudges easily. May require occasional polishing to maintain shine |
Matte (Aluminum, Stainless Steel) | Hides fingerprints and smudges well. Offers a subtle, understated style. Usually offers good grip during use | Can sometimes hold onto soap scum more than polished finishes. May require more frequent cleaning to retain its look |
Coated (Alloy, Bronze, Brass) | Available in various colors, enhancing customization. Can improve corrosion resistance. May offer additional grip compared to polished finishes. Alloy razors balance quality with affordability | Coating may wear or chip over time, especially with frequent use. May not be as durable as stainless steel or titanium |
Patina (Brass, Bronze) | Develops a unique and characterful appearance over time. Each razor ends up with a one-of-a-kind finish | Requires regular maintenance to prevent unwanted corrosion. Some users may not appreciate the aged look |
Keep these pros and cons in mind to make an informed choice that suits your personal style and shaving habits. Remember, the longevity of your razor largely depends on how well you take care of it, regardless of the finish.
Maintaining a Durable and Corrosion-Resistant Safety Razor
To maintain a durable and corrosion-resistant safety razor, proper cleaning and maintenance are essential. Regularly cleaning your razor after each use, replacing worn or damaged parts, and using appropriate storage methods can help extend the lifespan of your razor.
Proper Cleaning And Maintenance
To maintain a durable and corrosion-resistant finish on your safety razor, follow these essential cleaning and maintenance practices:
- Clean your safety razor after each use to remove any shaving cream, hair, and skin oils that can cause build-up and potentially lead to corrosion.
- Disassemble the razor head, handle, and base carefully to clean each part thoroughly with warm soapy water and a soft brush or cloth. Ensure all residue is removed from hard-to-reach areas.
- Rinse the parts under running water and dry them completely with a clean, dry cloth to prevent water stains or corrosion.
- Regularly inspect the razor for any signs of rust or corrosion and address them promptly. Afterward, apply an oil coating for protection.
- Store the disassembled razor in a dry place to avoid exposure to moisture, which can accelerate rust formation.
- Periodically check for loose parts or signs of wear, such as blade dullness or handle looseness, which can impact the performance of your safety razor. Replace worn or damaged parts as needed.
- Consider investing in a specialized metal polish if your safety razor’s finish requires restoration due to extensive wear or corrosion over time.
Related Post: How to Clean and Care for Your Favorite Double Edged Safety Razor
Conclusion
Choosing the right finish for your safety razor can be important. Different finishes, such as polished, matte, or coated, can significantly impact the razor’s durability and resistance to corrosion.
It’s essential to consider various factors like material and maintenance when making this decision. Proper care and regular maintenance play a vital role in extending the lifespan of your safety razor.
By understanding these influences, you can ensure that your safety razor remains durable and resistant to corrosion for years to come.
FAQs
1. What does the finish on a safety razor do?
The finish of a safety razor, like polished, matte, or coated surfaces, protects against corrosion and wear. It makes the razor more durable over time.
2. Why does the type of finish matter for resistance to corrosion?
Different finishes react with moisture and air differently; chrome-plated or heat-treated finishes can better resist rust and maintain their quality through excellent durability.
3. Can all metals used for safety razors be finished in the same way?
No, not all metals are alike—stainless-steel might take on a mirror-like polish while softer metals such as zamak suit other finishing techniques due to differences in hardness and malleability.
4. Does a coated finish affect how I should care for my razor?
Yes! Coated razors often have extra layers that prevent damage but may require special attention when cleaning to avoid scratching or wearing away these protective coatings.
Great review! Considering my 2 ABS plastic razors (Fine Superlite & & PAA Phantasm) deliver as close and comfortable a shave as my Wolfman did, it is head geometry, not metallurgy at play.
That said my early edition sintered Weber still beats every other one of my 20 safety razors.
I think this article completely misses the most important issue. Many razors, especially razor heads, are made out of zamac. Zamac will deteriorate if exposed to water. Heads for example will detach from the threaded rods that hold the head to the handle. The razor may also just deteriorate so much that it just can’t be used.
Essentially, the head becomes so pitted that the only way to describe it is that it just falls apart. Zamac razors are generally, and perhaps always, chrome plated. If the chrome plating fails, the razor will deteriorate. Many razors that are marketed as “brass” only have brass handles. The heads are often made of zamac. I won’t buy any more of these things and so without mentioning any names, many currently available razors are things I stay away from. Give me a vintage Gillette made entirely out of brass and chrome plated any day. I’ll also buy stainless steel or an entirely brass razor, but no chrome plated zamac for me.
Really, really. All that BS about razor material it really good info if your building a space shuttle. Guess what, an ordinary razor w/ chrome over alloy material will have more glide that your high dollar material. My stainless razors I sent in to Razor Emporium for plating over stainless & they outperform all the stainless razors. So before you get al foot w/ expensive razors remember the vintage Gillettes 100yrs old still in service,really-really your friend Fred H.
I have to say, I’m with you Fred. I have several zamac and/or brass razors )with who knows what finish) for many years. Some well over 20 years and one pre WW2 Gillette. I don’t really keep great care of my razors, judging by what I read from other posters. While I don’t toss my razors around, I have dropped them once or twice. I’ve never had even a spot of corrosion or anything break.
Other than the weight, length, balance and design of the head (ie, no blade issues), I really have no interest in the materiel used in its construction. If something happens to one of my razors (which I don’t anticipate) I can by 3, 4 maybe 5+ more for the same price as many/most stainless steel razors. Not to even talk about titanium. Then again, my razors have no collector (or snob) appeal.
But to each their own.
Good article; however, should include more than a single mention of aluminum (in a chart), and no specific mention of anodizing. Something to consider, should you decide to update down the road.